
Press ALT+F to fill in the back with polygons.Go to Select > Edge Loops to select the rest of the ring.Switch to edge select mode and select one of the outer edges.
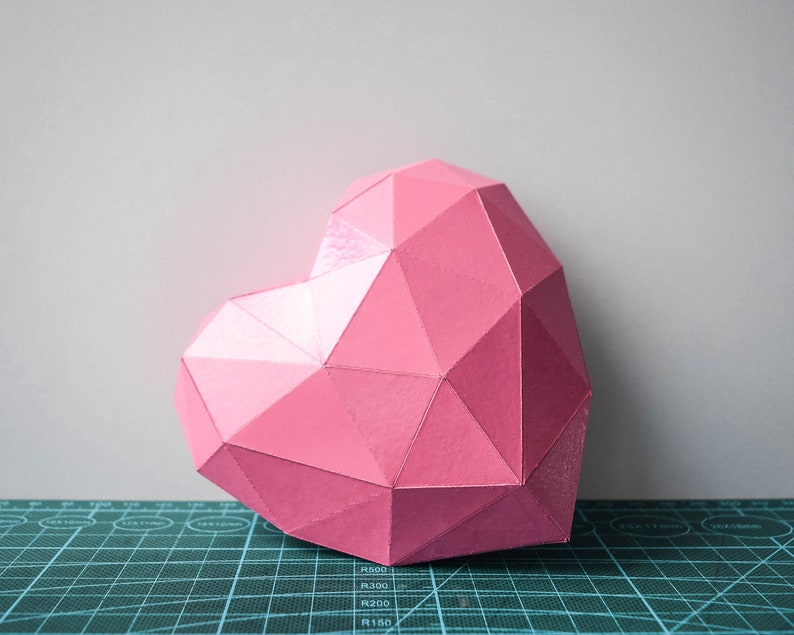
Here is an example where we don't even need to use the Solidify modifier.To do this, go to File > Export > Texture Editing > 3D Model with UV Info.First we will need to export the model from Pepakura Designer.Step 1: Export OBJ from Pepakura Designer A coworker of mine did a nice guide on using the same techniques for printing game models. This guide is written with pep files in mind, but I think a lot of it is applicable to printing game models or any other sort of meshes. I'm posting everything here, but you can also find it in a much nicer format at Blender is scary, but I hope this guide will be a good introduction for people who have never used it before. We're going to do all of this using Blender, a very powerful free tool for 3D modeling. getting the scaling right, adding some detail, and then cutting everything up into pieces small enough for printing. I'm going to cover cleaning up the models, giving them thickness. I didn't find any really thorough guides already, so I collected all the information on the problems I've run into and the techniques I learned to solve them, and put them in this tutorial. It turns out that 3D printing pep files is a lot harder than just converting them to STL and hitting print. After fastening all the aluminium together the cardboard was removed and smart pixel led strip lights installed in each channel.I've been working on 3D printing a Mark III Iron Man suit based on DancinFool's Pepakura files. Then we would assemble these together and cut lengths of aluminium LED diffuser channels to tape to the edges of the cardboard shape. To enlarge the design we projected the A4 plan through a roof mounted projector onto big fridge and bike boxes.

As well as this big mask we make 3 GIANT versions in a barn on the Matamata festival site. As well as the human sized masks I build a huge version to stay in the lab for experimenting with projection mapping. After about 4 iterations I was happy with the design and sent the plans out to the festival precipitants so they could print out the plans on an A4 printer and build their own. After cutting and assembling there would be changes after testing by wearing and handling the physical object, then making adjustments back in the 3Dmodel. (which can be fast is you use the select by appearance function). To complete this step I had to import the svg files into Illustrator and convert the lines into the correct colour and line type for laser cutting. After feeling happy with the designs I made in 3DsMax, I extracted the paper plan with Pepakura and laser cut it out.
